The Measurement of Residual Stress using Laboratory Based X-Ray Diffraction Instruments - Follow up
Workshop and Exhibition
Date/Time: 7 May 2025
Location: National Physical Laboratory, Teddington, UK
Delegate Fees (inc) VAT: £75 Member, £100 Non Member
This is a follow up to the 2023 meeting which will aim to discuss the practical aspects of the technique. Presentations from the 2023 event can be viewed here
Exhibition
Exhibitor places subject to availability at no charge, please contact the BSSM for further details
For more information contact the BSSM at info@bssm.org
Programme will include
• Troubleshooting; how to spot what’s gone wrong (if anything) and what to do about it.
• How to check that your diffractometer is working correctly.
• Layer removal, the practicalities. How to determine the measurement depth etc.
• How to measure rough surfaces, shot peened samples etc.
• Sample geometry; the effects of curvature, shadowing, complex, compound curves.
• Non-destructive detection of manufacturing defects.
• How to optimise your particular type of diffractometer.
• Preliminary results submitted as part of the Round Robin study proposed at the 2023 meeting
Demonstrations
The portable residual stress diffractometers will be working, with suitable shielding, of course. For safety reason, they will be fitted with chromium anode X-ray tubes.
Why not bring something to measure???
We will be able to measure ferritic steels, aluminium and magnesium alloys on the day of the meeting.
Exhibition
We will be having an exhibition with live X-Ray diffractometers again. If you are interested in exhibiting please contact the BSSM at info@bssm.org
Meeting Programme
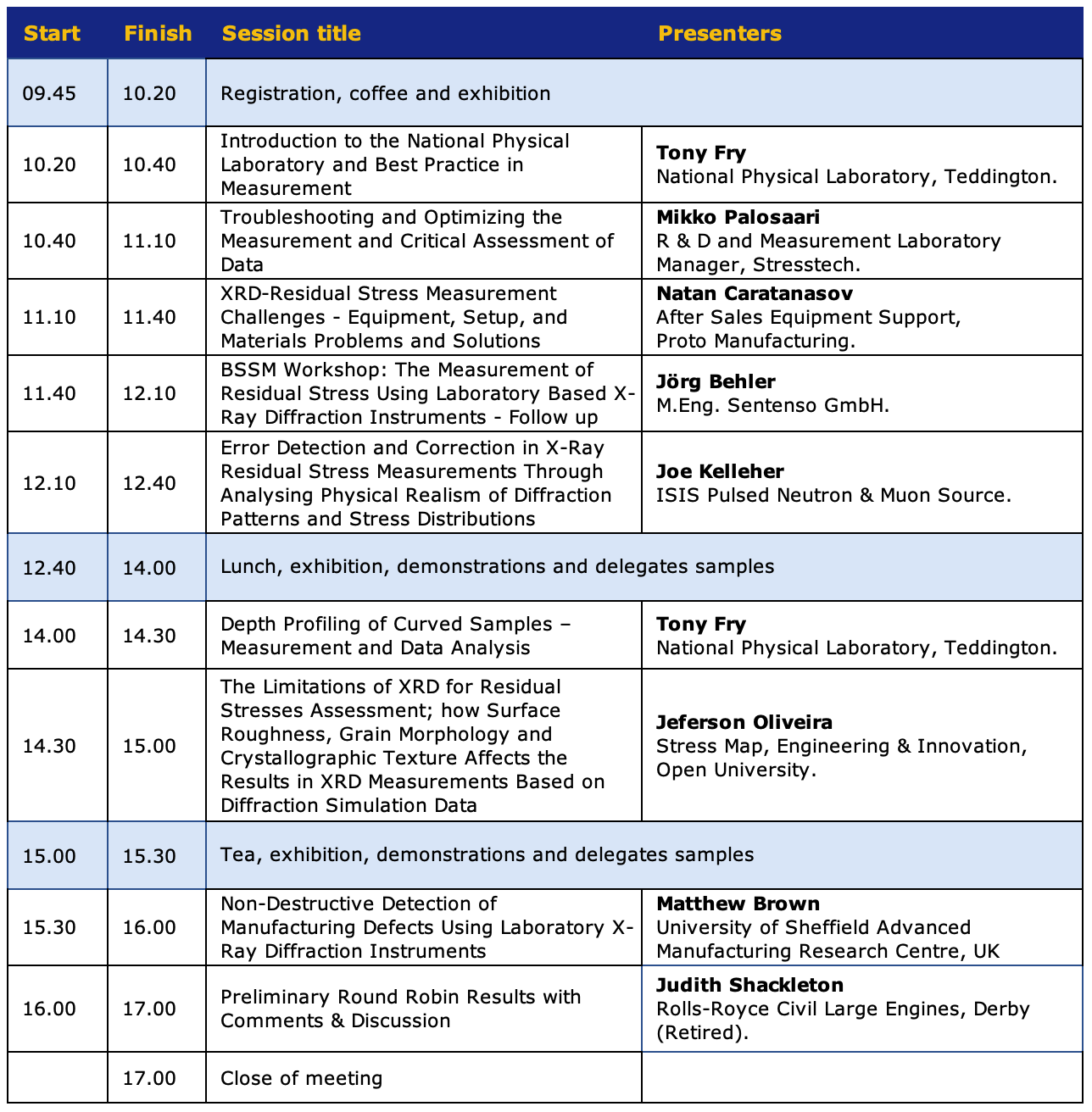
Speakers
Troubleshooting and Optimizing the Measurement and Critical Assessment of Data
Mikko Palosaari, R & D and Measurement Laboratory Manager, Stresstech
Evaluation of residual stresses (RS) by X-ray diffraction can lead to wrong or misleading results if the measurement process and the measured data are not critically assessed. Although standards like EN 15305 explain what needs to be taken into consideration when doing RS measurements, there are still subtle things that can go wrong. In this presentation some of the not so obvious root causes for unsuccessful measurement results are gone through and means of detecting and avoiding them are discussed.
Measuring Residual Stress on Curved Samples
Jörg Behler, Sentenso GmbH
This presentation will explore the limitations of existing equations for residual stress determination, which are typically applicable only to flat surface geometries. Samples need to be almost flat, because the laboratory equipment to measure residual stress does not track the location of the peaks gathered for stress determination but assumes a uniform flat surface for stress determination. The has also implications for certain kinds of waviness like turning marks. While these limitations are mostly known, what is the subject of debates is the question what can be considered a flat surface for a given measurement spot? The focus will be on the practical implications for everyday measurements and best practices for using cos-alpha devices. Insights will be drawn from relevant literature, established standards and findings from an ongoing Round Robin test that investigates this issue.
The Measurement of Residual Stress by Laboratory Based X-Ray Diffraction Methods
Judith Shackleton, BSSM
At the last meeting it was agreed to set up a new Round Robin test for the measurement of residual stress using laboratory-based X-ray diffraction methods.Two sets of samples were kindly donated. There are four, small shot peened titanium samples and four larger pieces of machined, ferritic steel. None of these sample are easy to measure. The samples have now been distributed around the UK. The X-ray tube anode and the reflection, {hkl} to measured was specified in the work sheets for consistency. Several sets of results have now been submitted. It's not proposed to discuss the absolute values of the results as the samples have still to be sent overseas though the relative values will be compared.
Depth Profiling of Curved Samples – Measurement and Data Analysis
Tony Fry, M.J. Lodeiro and R. Williams, National Physical Laboratory, Teddington, UK
Depth profiling of residual stresses using XRD is a well-established technique, straightforward to apply on large, flat surfaces using electropolishing. Challenges are presented in cases where parts are small volume, highly curved and where the stress field changes rapidly through the depth - particularly close to the surface. In these instances, it is essential to control the depth, and uniformity of material removal and to define the measurement depths accurately and consistently.
Work carried out at NPL on determining the residual stress depth profile of the nitrided outer surface of a 6 mm diameter cylindrical samples has encountered and sought to resolve many of these issues, resulting in improved depth analysis.
Samples were marked on the unaffected surface to define an exact position to remeasure with XRD in between each material removal step. 3D polymer additive manufacturing was used to create an electrolyte vessel and part support base closely matched to the part geometry, with repeatable electrolyte height, electrode depth and alignment used to ensure repeatable material removal on consecutive steps. Non-linearity in the surface topography was present in all axes so to define a reference surface and to accurately determine the removal depth, an Alicona 3D microscope was used to take consecutive height profiles of a defined line crossing through the electropolished region. These profiles were then repeatably aligned, based on the unaffected regions, with this region compared to the average of the data points within the depth plateau at the base of the removed material. Details of the method and resulting analysis are presented.
The Limitations of XRD for Residual Stress Assessment
Jeferson Oliveira, Stress Map, Engineering & Innovation, Open University, UK.
How surface roughness, grain morphology and crystallographic texture affects the results in XRD measurements based on diffraction simulation data.
XRD-Residual Stress Measurement Challenges - Equipment, Setup, and Materials Problems and Solutions
Natan Caratanasov, After Sales Equipment Support, Proto Manufacturing.
A discussion will be presented detailing the issues which arise when XRD-residual stress measurements are attempted and either the equipment setup, or sample itself result in difficulties in obtaining good measurements. The ways of distinguishing between these issues will be discussed.
Error Detection and Correction in X-Ray Residual Stress Measurements Through Analysing Physical Realism of Diffraction Patterns and Stress Distributions.
Joe Kelleher, ISIS Pulsed Neutron & Muon Source
Laboratory X-ray diffraction offers a widely applicable means of mapping residual stresses over the surface of metallic materials. The sin2psi method offers a solution to the ever-present d0 problem in X-ray stress measurement, with macroscopic elastic constants typically being the only required external input to get stress from the measured data. However, errors may still arise from sample or instrument misalignment, limitations in the measured input data (e.g. number and range of psi tilts), improper surface preparation for stress measurement, or material microstructure issues like texture or large grain sizes.
These errors may become apparent at any stage of the data processing pipeline: from the shape and quality of fit for the individual diffraction peaks, through the shape of the sin2psi plots for each measurement location, right through to the overall distribution of measured stresses across the measured surface.
This talk will focus on techniques for detecting and correcting these errors, moving beyond the analysis of individual data points to assess the physical plausibility of the overall residual stress distribution. Inconsistencies such as non-equilibrium stress states or unphysical stress gradients can indicate systematic errors and measurement artifacts in residual stress results. Routes to identifying, quantifying and ideally correcting such issues are discussed, with a view to ensuring that reported stress distributions accurately reflect the true internal state of the material.
Non-Destructive Detection of Manufacturing Defects Using Laboratory X-Ray Diffraction Instruments
Matthew Brown - University of Sheffield Advanced Manufacturing Research Centre, UK
The measurement of fatigue life limiting manufacturing defects such as white layers, plastic deformation of the near-surface and grinding burn is possible with laboratory based residual stress X-ray diffractometers. The phenomenon of diffraction peak broadening due to crystallite size and strain effects in the machining affected region allows for the detection of manufacturing defects in real engineering components through broadening or narrowing of the same diffraction peaks employed in the sin2psi method.
This talk will discuss the methodology and accompanying validation studies which have been carried out comparing the technique against the inherently destructive industry standard microstructural cut-up method. Results from a round robin investigation of the X-ray technique show how the technique can be readily transferred across different lab-based diffractometers via appropriate calibration.